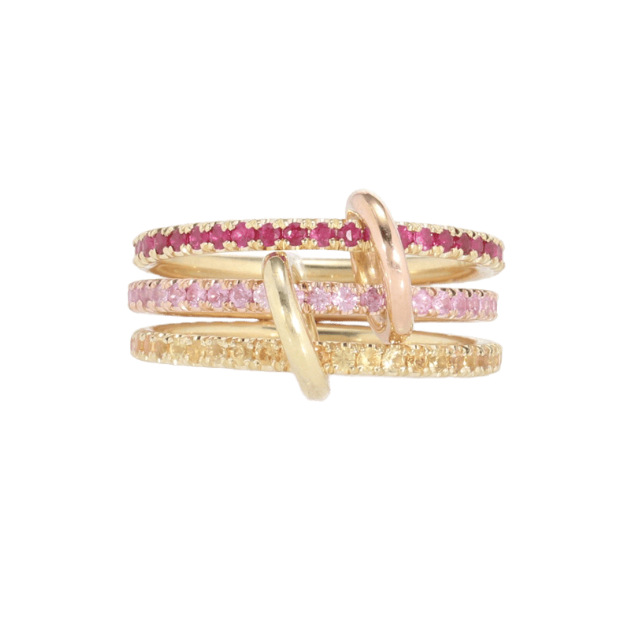
本身
html
925 Silver Triple Hoop Ring Set with Round Zirconia – Rose Gold & Gold Vermeil Stackable Bangles for Women
Elevate your jewelry collection with the stunning 925 Silver Triple Hoop Ring Set, featuring delicate round zirconia accents and elegant rose gold or gold vermeil overlays. This minimalist yet eye-catching set is designed for women who appreciate timeless beauty and versatility in their accessories.
Exquisite Design & Craftsmanship
Each piece in this set showcases:
- Three perfectly proportioned sterling silver hoops
- Sparkling round-cut zirconia stones for subtle brilliance
- Premium rose gold or gold vermeil overlays for luxurious contrast
- Lightweight, comfortable wear for all-day elegance
Versatile Stacking Options
The beauty of these stackable bangles lies in their adaptability. Wear them together for a bold statement or mix and match with your existing jewelry collection. The minimalist design makes them perfect for:
- Office wear – professional yet stylish
- Evening events – effortlessly chic
- Casual outings – subtle sophistication
- Special occasions – understated glamour
Premium Materials for Lasting Beauty
Crafted from 925 sterling silver, these hoops offer durability and tarnish resistance. The gold vermeil and rose gold overlays provide a luxurious finish without compromising quality. Each zirconia stone is carefully set to maximize its sparkle while maintaining the piece’s sleek profile.
Perfect Gift for Any Occasion
Whether you’re treating yourself or surprising someone special, this triple hoop ring set makes an ideal gift for:
- Birthdays
- Anniversaries
- Graduations
- Just-because moments
Presented in an elegant gift box, this jewelry set is ready to impress from the moment it’s received.
Care Instructions
To maintain your jewelry’s beauty:
- Store in a dry, airtight container when not in use
- Avoid contact with perfumes, lotions, and harsh chemicals
- Clean with a soft jewelry cloth as needed
- Remove before swimming or showering
With proper care, your 925 Silver Triple Hoop Ring Set will remain a cherished part of your jewelry wardrobe for years to come.