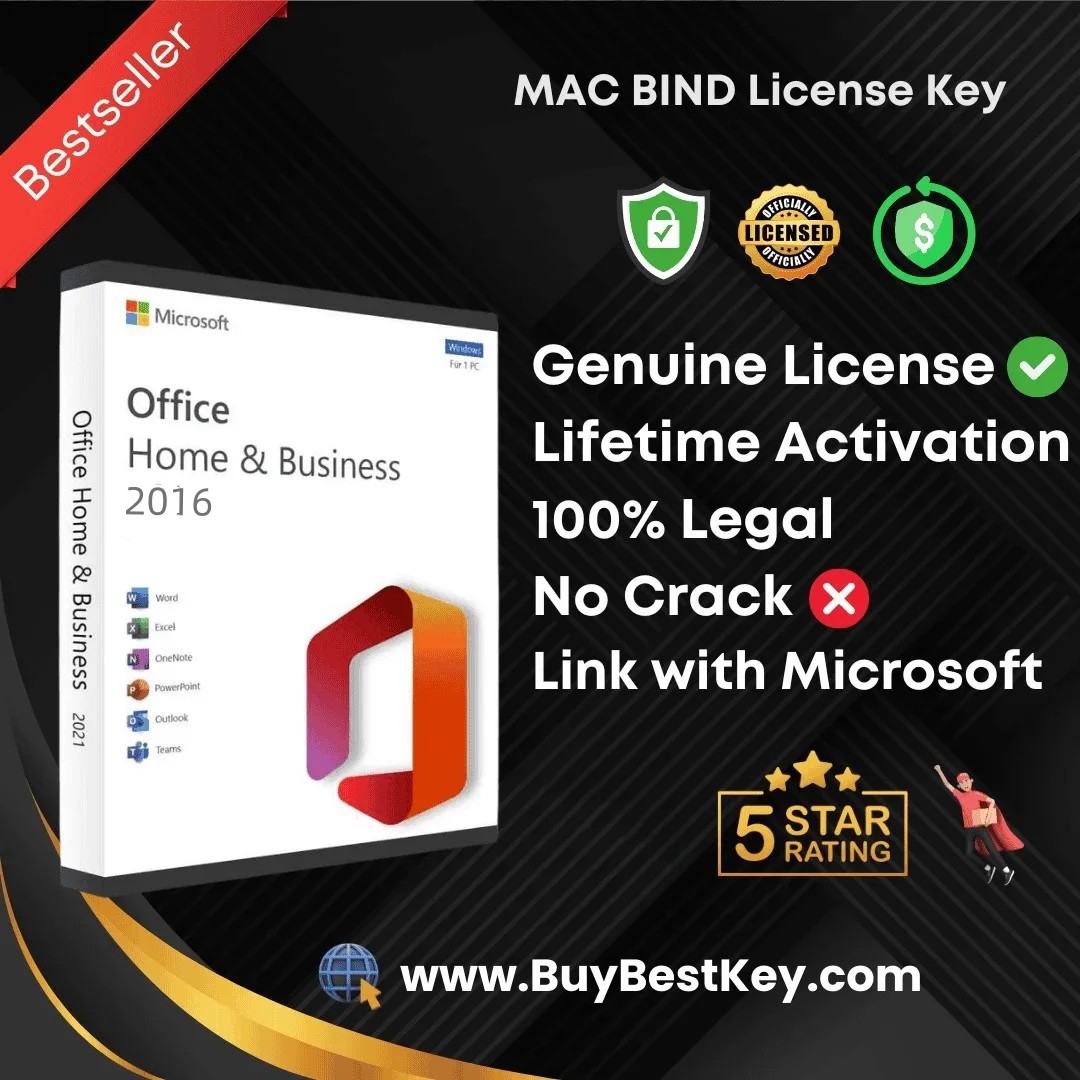
# Microsoft Office Product Key Activation Guide
## Introduction to Microsoft Office Product Keys
Microsoft Office product keys are essential for activating your software and unlocking all its features. These 25-character alphanumeric codes verify that your copy of Office is genuine and properly licensed. Whether you’ve purchased Office online or received it with a new computer, activating your product key is a crucial step in the installation process.
## Where to Find Your Microsoft Office Product Key
Your product key location depends on how you obtained Microsoft Office:
– Retail purchases: Check the product packaging or card inside the box
– Digital purchases: Look in your email receipt or Microsoft account
– Pre-installed versions: Often found on a sticker on your device
– Volume licensing: Contact your organization’s IT administrator
## Step-by-Step Activation Process
### Method 1: Online Activation
1. Open any Office application (Word, Excel, etc.)
2. Click “File” > “Account”
3. Select “Activate Product” or “Change Product Key”
4. Enter your 25-character product key when prompted
5. Follow the on-screen instructions to complete activation
### Method 2: Phone Activation
1. If online activation fails, choose “Phone Activation” instead
2. Call the Microsoft activation center number provided
Keyword: microsoft office key
3. Provide the installation ID displayed on your screen
4. Enter the confirmation ID you receive from Microsoft
## Troubleshooting Common Activation Issues
If you encounter problems during activation, try these solutions:
– Check your internet connection
– Verify you’ve entered the key correctly (no dashes needed)
– Ensure you’re using the correct version of Office for your key
– Contact Microsoft Support if you suspect your key is invalid
## Managing Your Office Subscription
After successful activation, you can:
– View your subscription status under “File” > “Account”
– Install Office on additional devices (depending on your license)
– Renew your subscription before it expires
– Deactivate installations when needed
## Important Security Considerations
Always purchase Microsoft Office product keys from authorized retailers to avoid:
– Counterfeit software
– Malware risks
– Invalid or already-used keys
– Potential legal issues
Remember that Microsoft never sends product keys via unsolicited emails or pop-up ads. If you suspect you’ve received a fraudulent key, contact Microsoft Support immediately.