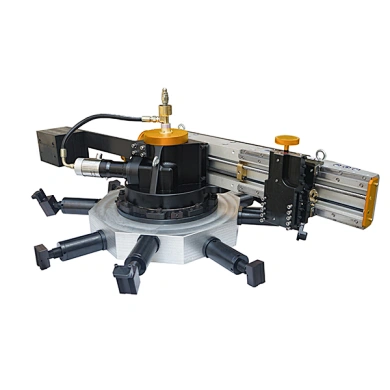
# Industrial Flange Facer: Essential Tool for Precision Machining
What is an Industrial Flange Facer?
An industrial flange facer is a specialized machine tool designed for resurfacing and machining flange faces to ensure proper sealing and alignment in piping systems. These powerful machines play a critical role in maintaining the integrity of industrial piping networks across various sectors including oil and gas, petrochemical, power generation, and shipbuilding industries.
Key Features of Modern Flange Facers
Today’s industrial flange facers incorporate several advanced features that make them indispensable for precision machining:
- Portable designs for on-site machining operations
- High-torque motors for efficient material removal
- Precision alignment systems for accurate face preparation
- Versatile cutting tool configurations
- Digital measurement and control systems
Applications in Various Industries
The versatility of industrial flange facers makes them valuable across multiple sectors:
Oil and Gas Industry
In pipeline construction and maintenance, flange facers ensure leak-proof connections critical for safety and environmental protection.
Keyword: Industrial flange facer
Power Generation
Power plants rely on flange facers to maintain steam and water piping systems that operate under extreme pressures and temperatures.
Marine Applications
Shipbuilding and repair operations use flange facers to maintain piping systems that must withstand harsh marine environments.
Benefits of Using Professional Flange Facing Equipment
Investing in quality industrial flange facers provides numerous advantages:
- Improved Safety: Properly machined flanges reduce the risk of leaks and system failures
- Cost Savings: On-site machining eliminates the need for component removal and replacement
- Time Efficiency: Quick setup and operation minimize downtime in critical systems
- Precision Results: Achieve surface finishes and tolerances required for optimal sealing
Maintenance and Care Tips
To ensure long-term performance of your industrial flange facer:
- Regularly clean and lubricate moving parts
- Inspect cutting tools for wear and replace as needed
- Store the machine in a dry, protected environment
- Follow manufacturer’s guidelines for calibration and maintenance
- Train operators in proper usage techniques
Choosing the Right Flange Facer for Your Needs
When selecting an industrial flange facer, consider these factors:
- Size range of flanges you need to machine
- Available power source at your work sites
- Required precision levels for your applications
- Portability requirements
- Budget constraints and long-term value
Modern industrial flange facers represent a significant advancement in field machining technology, offering reliable solutions for maintaining critical piping infrastructure across industries. By investing in the right equipment and proper training, organizations can significantly improve their maintenance capabilities while reducing downtime and operational costs.